Aluminum is one of the most versatile and widely used metals across multiple industries — from construction and transportation to electronics and renewable energy. Its combination of lightweight properties, durability, and corrosion resistance makes it an ideal choice for a wide range of applications. But when it comes to getting aluminum parts shaped to precise specifications, aluminum extrusion factory becomes the go-to process. That’s where a top aluminum extrusion factory makes all the difference.
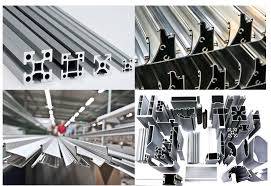
In this article, we’ll explore what makes an aluminum extrusion factory stand out, why precision profiles and custom solutions matter, and how to choose the best partner for your aluminum needs.
What Is Aluminum Extrusion?
Aluminum extrusion is a process in which aluminum alloy material is forced through a die with a specific cross-sectional profile. It’s similar to squeezing toothpaste from a tube — the shape of the opening determines the shape of the extruded material. After extrusion, the profiles are cooled, straightened, and cut to the required lengths. Additional finishing processes like anodizing, powder coating, or machining may follow depending on the end-use.
This method allows for complex, custom-designed shapes and ensures structural integrity and design flexibility, which is why it’s so widely adopted.
Characteristics of a Top Aluminum Extrusion Factory
Not all extrusion factories are created equal. The best aluminum extrusion facilities stand out in several key ways:
1. Precision Engineering and Quality Control
Precision is the heart of modern manufacturing. A top-tier factory utilizes advanced CAD/CAM software, automated machinery, and CNC-based finishing techniques to deliver exact measurements with tight tolerances. These factories also implement rigorous quality control processes at every stage — from billet selection to final inspection — ensuring that the products meet or exceed industry standards such as ISO, ASTM, or RoHS compliance.
2. Customized Solutions
Standard profiles don’t always cut it. Many industries — such as aerospace, automotive, electronics, and architecture — require custom extrusions to meet specific engineering demands. A leading factory collaborates with its clients closely to design and manufacture unique profiles that meet highly specialized applications. From choosing the right alloy to designing complex multi-void shapes, customization is a key differentiator.
3. Modern Equipment and Technology
Leading extrusion factories invest in state-of-the-art equipment, including:
High-tonnage extrusion presses (600–4,000 tons)
On-site die manufacturing and repair units
Heat treatment and aging ovens
Automatic stretching and cutting machines
Surface treatment lines (anodizing, powder coating, etc.)
Such capabilities enable them to produce high volumes efficiently while maintaining consistent quality.
4. Sustainability Practices
As industries move toward greener practices, aluminum extrusion factories are also shifting toward sustainability. The best factories use recycled aluminum, energy-efficient machinery, and waste-reduction protocols. They often have certifications like ISO 14001 for environmental management, ensuring minimal ecological impact.
5. Industry Expertise and Reliable Support
Experience matters. A factory with decades of industry expertise knows how to avoid common pitfalls, optimize material usage, and meet tight production deadlines. Excellent customer support, responsive communication, and post-sale assistance are all hallmarks of a top aluminum extrusion partner.
Applications of Precision Aluminum Profiles
Customized and precise aluminum profiles find their way into a vast number of applications across sectors:
1. Construction and Architecture
Aluminum extrusions are used in window frames, curtain walls, structural glazing, louvers, railings, and modular partition systems. Their sleek look and corrosion resistance make them perfect for both structural and decorative purposes.
2. Automotive and Transportation
Aluminum helps reduce vehicle weight, enhancing fuel efficiency and performance. Extruded profiles are used in frames, crash-management systems, heat exchangers, and EV battery trays.
3. Electronics
Precision extrusions are ideal for heat sinks, enclosures, and connectors in electronic devices. Aluminum’s excellent thermal conductivity and lightweight nature make it a great choice.
4. Industrial Equipment
Machinery frames, conveyor systems, and assembly lines often rely on aluminum profiles for modularity and robustness.
5. Solar and Renewable Energy
Mounting systems for solar panels often feature extruded aluminum parts that are durable, corrosion-resistant, and lightweight for rooftop or ground installation.
The Role of Custom Solutions in Product Innovation
Innovation often begins with customization. Whether it’s developing lightweight drone frames or intricate medical device components, custom aluminum extrusions allow for:
Enhanced functionality through purpose-built designs
Material optimization for strength and weight reduction
Integration of multiple components into a single extruded shape
Improved aesthetics with smoother, streamlined surfaces
Faster assembly due to interlocking or modular features
By partnering with a factory that excels in custom solutions, manufacturers can accelerate product development, reduce production costs, and achieve higher performance.
Choosing the Right Aluminum Extrusion Factory
Here’s a quick checklist to help you select the best aluminum extrusion factory for your project:
1. Experience & Reputation
How long has the factory been in operation? Do they serve your industry niche? Look for customer testimonials, case studies, or certifications to validate their expertise.
2. Design Assistance
Can their engineers help you optimize your design? Do they provide 3D models, stress analysis, or prototyping services?
3. Production Capacity
Does the factory have the capability to meet your required volume — both low-run prototypes and high-volume production?
4. Tooling and Die Capabilities
Can they manufacture custom dies in-house? What’s the lead time for tooling?
5. Range of Alloys
Different alloys suit different needs. A good extrusion partner offers a wide range — such as 6061, 6063, 6082, and 7075 — each with distinct mechanical properties.
6. Finishing Services
Do they offer surface treatments like anodizing, powder coating, or painting? Can they provide secondary operations such as drilling, punching, or cutting?
7. Lead Time & Logistics
Are they able to deliver within your deadlines? Do they offer global shipping or local support?
8. Sustainability Practices
Do they prioritize the use of recycled aluminum? Are they compliant with environmental and safety standards?
Case Study: Excellence in Action
Let’s take a look at a hypothetical but realistic example of a top-performing aluminum extrusion factory: Alumatech Industries.
Overview:
Based in a tech-industrial hub, Alumatech Industries operates with over 35 years of experience in precision aluminum extrusion. The company serves over 20 industries worldwide and handles everything from design consultation to finishing and logistics.
Key Capabilities:
8 extrusion presses (ranging from 800 to 3,500 tons)
On-site die shop for quick turnaround on custom profiles
20+ alloys in inventory
CNC machining and laser cutting
Automated anodizing and powder coating lines
ISO 9001 and ISO 14001 certifications
Recent Project Highlight: Alumatech recently collaborated with an EV manufacturer to design a battery cooling tray that integrated structural supports and coolant channels into a single extruded part. This reduced part count by 60%, lowered vehicle weight by 15%, and simplified the assembly process — a win for both cost and performance.
This case exemplifies how working with the right factory can lead to innovations that drive product and business growth.
Conclusion
Aluminum extrusion is more than just shaping metal — it’s about enabling possibilities. Whether you’re creating lightweight automotive parts, sleek architectural elements, or precision industrial components, your choice of aluminum extrusion factory plays a critical role in the success of your project.
A top factory delivers precision, quality, and customization with reliability, helping you bring your ideas to life. From engineering support and advanced equipment to sustainable practices and expert guidance, partnering with a leading extrusion provider is a smart move in today’s competitive market.